A Milestone in Advanced Manufacturing
L&H Industrial has recently undertaken a significant project: installing one of the largest vertical turning lathes (VTL) in the nation at their Tempe, AZ manufacturing center. This project marks a new era in L&H’s capacity to serve its global customers across heavy industries.

the planning
installing one of the biggest vertical turning lathes in the country
L&H Industrial’s recent purchase of a massive vertical turning lathe began with 21 semi-truck loads of the machine’s components transported to Tempe, AZ, and spanned nearly two years, from purchase to completing final testing.
The project management of a machine install of this scale required hours of planning and selecting trusted vendors to support specific needs on the project that were critical to ensuring the machine would be installed precisely.
Kaela Torres, Engineering Manager for L&H’s Tempe, AZ manufacturing facility, was asked to manage the project because of her attention to detail, leadership, and experience in project management. Torres prioritized tasks based on lead times and collaborated with teams both internally and externally to ensure the project’s success. Key priorities included transporting and storing the machine components, designing and constructing the foundation, upgrading the power supply, and obtaining necessary permits.
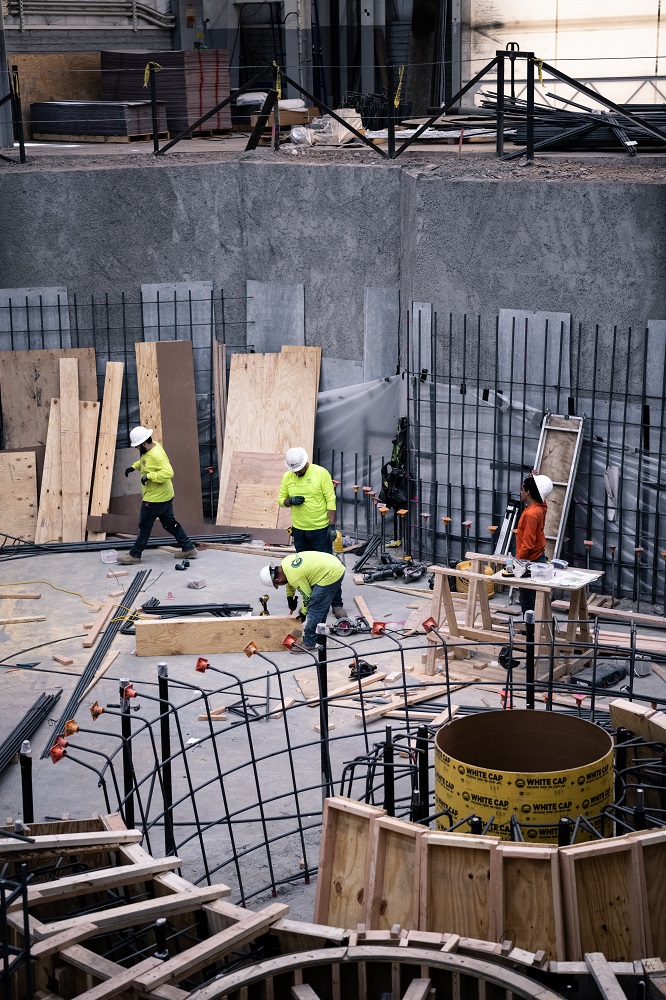
strategic partners to overcome challenges
critical steps to complete a massive machine install
Like any project, it wasn’t completed without some challenges along the way. Despite these challenges the project was completed successfully with the collaboration of teams ensuring critical details were checked, appropriate documentation was collected, and learnings were shared with the team.
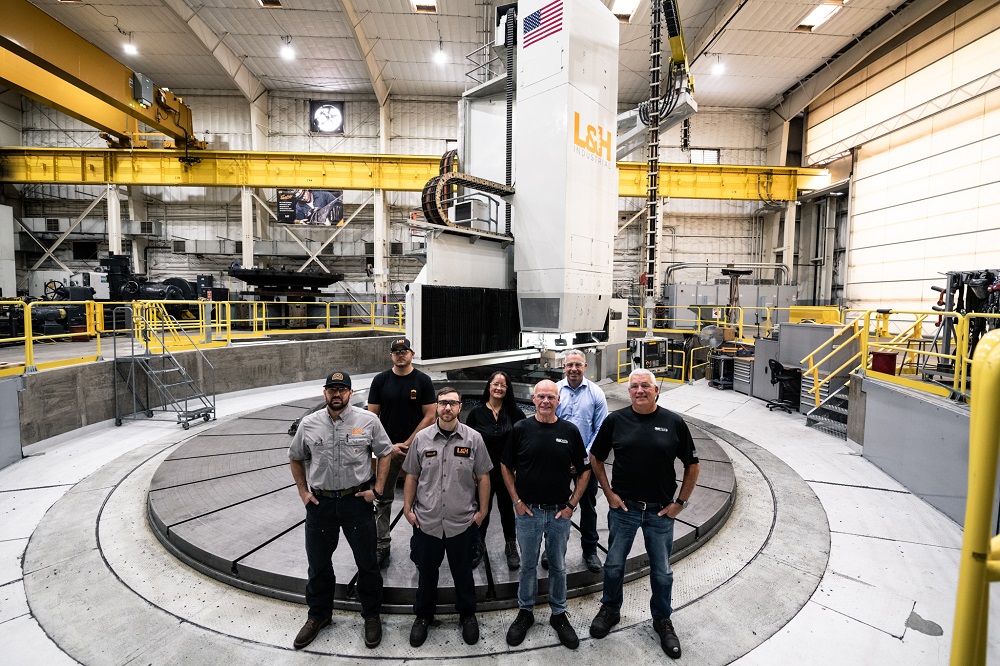
Team Machine Tools, who specializes in machine retrofits, rebuilds, and relocations, was selected as a partner to disassemble, transport, and install of the machine in Tempe, AZ. A team was then relocated from the company’s headquarters in Canada to live onsite at L&H’s Tempe location for eight months of the project. With decades of experience in large complex machine installs and relocations of critical assets, Team Machine’s president, Cam Allen, expressed, “This is by far the largest project we have undertaken.”
Unisorb, a company that specializes in installation solutions for vibration isolation, mounting, alignment, anchoring, and grouting, was selected by Torres to design a sufficient foundation for the machine. In 7 months Unisorb designed a complex foundation along with all the isolation materials, fixators and other materials needed for such a substantial foundation design. The foundation required excavating a hole in Tempe’s machine shop that was 80-feet by 80-feet and 22-feet deep and over 2,100 cubic yards of concrete was poured in 6 major pours over the span of 9 months. The foundation itself weighed in at more than 8.1 million pounds.
Basalt Building Group was contracted as the general contractor for the project and oversight of specific critical tasks including demolition, temporary wall shoring, concrete pouring, excavations and all steel reinforcement which utilized approximately 263,000 lbs. of steel. Russell Henry with Basalt explained the importance of these tasks to ensure the successful installation of a super calibrated machine with little tolerance. “It ensures precision, controls vibrations, extends the machine’s lifespan, enhances safety, and boosts efficiency and productivity,” added Henry.
After inspecting the current power available, it was determined it was not sufficient and the new machine would require a power upgrade, which added another critical step to the project. With the recommendation of L&H’s facility electrician, Travis Dykstra, Torres began working with electrical engineering firms, architectural engineers, the City of Tempe, electrical contractors, inspectors, hydrovac crews and more.
Torres highlighted the importance of planning ahead, anticipating long lead times, and maintaining open communication with all stakeholders as she reflected on the project and the major challenges along the way.
Enhancing ACCURACY and efficiency
Power and precision at scale
The massive new technology investment significantly expands L&H Industrial’s manufacturing capabilities. It allows for handling larger and more complex components, improving manufacturing times and efficiencies for common products like shovel swing systems, crushers, mills and turbines. The machine can perform multiple functions in a single setup, reducing the need for additional machinery and handling.
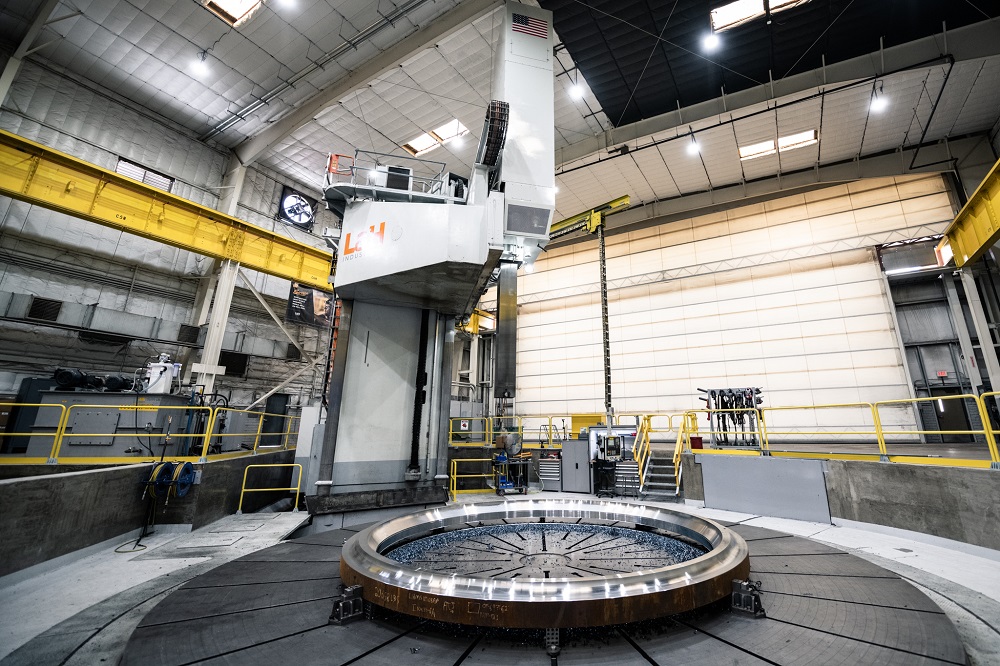
Additionally, the machine can handle up to 250 tons on its massive table, swing parts almost 42 feet in diameter, and turn parts over 16 feet in height. Unlike standard VTLs, this machine boasts live tooling for additional milling, drilling and tapping functions, broadening its utility. This capacity, combined with a highly skilled team of machinists and advanced tooling and software, enhances L&H’s ability to manufacture massive components with precision and ease.
competitive advantage
a strategic move to support the biggest machines on earth
As one of the few companies in the US with such advanced machinery, L&H Industrial gains a significant competitive advantage. The VTL enables the company to take on more complex projects, which is nearly impossible to find a similar capability within the US. This advantage translates to reduced transportation costs and minimized downtime for customers, enhancing overall efficiency.
The successful installation of the VTL stands as a testament to L&H Industrial’s dedication to innovation and excellence in serving their customers. With this advanced machinery, L&H is well-equipped to meet the evolving needs of their global customers and continue pushing the boundaries of what is possible in heavy industry manufacturing.
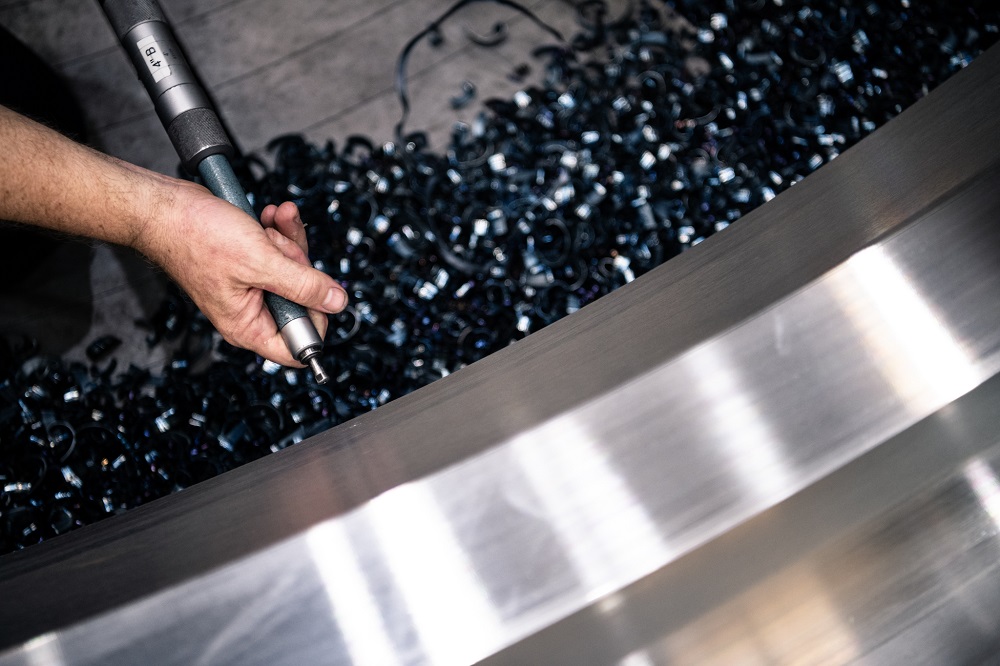
– KAELA TORRES, ENGINEERING MANAGER
L&H knew that within our arsenal we needed a larger machine, and with customers expecting you to hit plus or minus two thousandths or plus or minus five thousandths of an inch, we are able to maintain those on really large parts – putting us on a different level.
Check out the Details on this massive machine
Want to know more?
Reach out. This colossal machine is online and our teams are ready to bring next-level accuracy to components and assemblies at scale.